PTAW AND GTAW (TIG) TECHNOLOGY COMPARED
What characteristics differentiate the PTAW welding process from the GTAW (or TIG) process?
The Plasma Transferred Arc Welding both with powder or wire as filler material is a welding process that produces a metallurgic bond only in part similar to GTAW (or TIG). The characteristics of the deposit are, indeed, considered superior.
The special characteristics of the PTAW welding process that differentiate it from all the others are first of all the presence of two separately controllable welding arcs: the pilot arc and the transferred arc.
Plasma Transferred Arc Welding: The Pilot arc
The pilot arc strikes inside the welding torch between the tungsten electrode and the copper nozzle activated by the button on the control panel. This pilot arc or plasma arc remains lit for the duration of the welding and is crossed by neutral gas (Argon) which, due to the temperature of the electric arc of about 5000, loses electrons and ionizes producing further energy and increasing its temperature up to 10,000-20,000 ºC.
By closing the torch-piece circuit you get the arc transferred with the plasma column (which in the torches passing through a nozzle bottleneck assumes the final shape of a cylindrical column) High directionality and energy density with variable temperature between 10,000 and 20,000 / C – maximum divergence angle 5 µ easily controllable through the amount of gas running through the pilot arc.
This characteristic of PTAW welding, unique among all welding processes, produces a precise control of penetration, particularly appreciable in the anticorrosion welded coating. The deposited layer can vary from 1.5 mm to 4 mm.
GTAW (or TIG) welding: what are the differences?
GTAW welding (also known as TIG) involves the use of an infusible tungsten electrode, protected by an inert gas, with or without filler metal.
In particular, the electric arc of a GTAW torch has a temperature of 5,000 ºC (compared to 10,000 and 20,000 ºC of PTAW welding) which is transmitted directly on the workpiece and is controllable only by the power of the welding machine. Moreover, the GTAW welding process does not include a cylindrical arc column, but is characterized by a conical bell whose vertex is the tip of the electrode and whose temperature decreases from the center to the periphery of the cone on the piece.
For the above reasons, PTAW welding technology can be considered an evolution of the GTAW (Tig) process
ADVANTAGES OF PTAW TECHNOLOGY OVER GTAW IN WELDED HARDNESS
The economic advantage is especially evident in terms of the higher welding speed of about three times and with the higher arc temperature that produces a higher deposit rate while keeping the temperature of the workpiece low.
On the operating side the tip of the tungsten electrode in the PTAW process remains intact for at least 8 hours as the arc strikes inside the torch on the conical part of the sharpening and not at the tip, while that of the GTAW torch the tip decays progressively already from its ignition reducing stability and controllability of the arc.
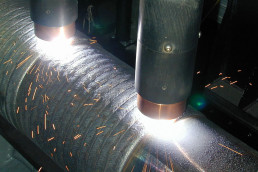
The metallurgical quality of the deposit: thanks to the penetration control, mixing with the base metal is practically irrelevant as it is minimal.
Temperature and arc density make the passage faster and less the localized stay of the arc on the workpiece and allow a faster cooling of the seam to the advantage of the fine grain metallurgical structure of the welding deposit, At the same time limiting the size of the thermally altered zone (ZTA).
An additional advantage of penetration control is, for example, the coating on petrochemical valves with Inconel 625, to keep the iron content at 0.5 mm from the interface on average, reducing the thickness of the coating drastically.
PTAW APPLICATIONS IN WELDED HARDNESS
Coatings on extruders
Coatings on blades for geothermal turbines
Coatings of and on high speed steels
tungsten carbide coatings. They are incorporated into the matrix then infusible.
Carrying screws and separators, parts of mixers, drilling tools
Protective bushings for woodworking
Reports on pulp mills paper
Coatings on forming dies for mould steels
Coatings on hot shear blades
Bearing layers for hard alloys
amagnetic carry-overs
coatings on products of any nature resistant to wear and corrosion.
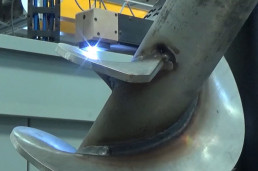
Carrying screws and separators, parts of mixers, drilling tools
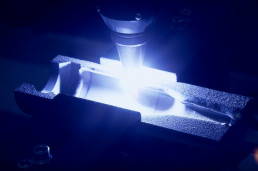
Coatings on stamps and spare parts for glass
What are the advantages of PTAW technology in joining welding?
- Instant, non-contact ignition of the welding arc and perfectly visible weld zone thanks to the generous distance between torch and workpiece.
Regular and uniform seam surface. - Excellent edge anchoring
- Minimum distortion of parts due to limited heat input.
- Greater operational flexibility when using powder due to the absence of the wire encumbrance.
- The arc column with a high concentration of energy allows you to carry out the background cyanide at full penetration ( Key hole) maintaining an arc distance such as to substantially improve the operation.
- Joining any metal with the PTAW process with either powder or wire intake is easy to perform, ensures consistent results and fast and economical.
What filler materials are used in the PTAW process?
Il processo PTAW Polvere si caratterizza anche per grande disponibilità di materiale di apporto in polvere, molto superiore rispetto al filo. La polvere infatti si produce atomizzando direttamente la materia prima, mentre per ottenere filo si deve subire processi di laminazione e di trafilatura costosi soprattutto per le superleghe.
Collateral
The PTAW Powder process is a benchmark in the nuclear, glassware, automotive valve and other high-end technology industries where reliable, safe and repetitive performance is needed.
Commersald is considered one of the world’s largest manufacturers of automatic PTAW systems. Our plants are designed and entirely produced for both the mechanical, electrical, electronic and application software within our, for 15 years now our plants are present worldwide, They often work continuously without interruptions and our customers continue to renew their fleet by purchasing our new plants.